Profile: Dan Blank, CEO & Co-founder, Toggle Industries
Dan Blank’s passion for designing and building large-scale projects has early roots. He grew up playing with Legos, always aspiring to build the next biggest thing– be it a Monorail, a ship, or even a model city. In the years since, he has charted his own course designing and manufacturing infrastructure. Today, he is the CEO and Co-founder of Toggle Industries where his mission is to make large scale civil and urban infrastructure projects more accessible to the communities that need them most. Toggle develops robotics and digital fabrication for the construction industry – starting with rebar for reinforced concrete – and aspires to reinvent the way we build our world. We caught up with Dan to learn more about his path to rebar and robots, and the challenges of innovating in the construction industry.
What life experiences brought you here today, and specifically when did you decide to become an entrepreneur?
I grew up in Western Massachusetts, I lived there my entire life in a college town. My mother is from the Philippines. My father grew up on Long Island in a New York Jewish community, and they met working in the medical profession.
Growing up, I was always into building things; problem solving with physical context. I was also into design, like graphic design, industrial design, architectural design, fashion. I definitely was attuned to the way things were made, and why they looked a certain way. And the entrepreneurial part… I was one of those kids who grew up selling whatever I could sell:mowing lawns, shoveling driveways, selling lemonade, all of that stuff.
Fast forward 25 years, and I’m at a graphic design agency working with an energy company that built and operated power plants. I got the opportunity to visit their construction sites, and one of them was for a wind farm. I saw workers building foundations for wind turbines out of reinforced concrete. That was really where I first got to see this process of what building with rebar and concrete entails, and how labor intensive this work is. And this is the way it’s always been done. It was a classic, “there’s got to be a better way to do this” type of moment. Seeing steel bars being put in place one at a time by hand 5000 times, over and over again, just for a single wind turbine foundation got my gears spinning.
Why rebar?
It seems like such a random and mundane thing. But it really is the basic building block of the whole built environment because reinforced concrete is by far the most consumed construction material. And it’s the material that all our structures and infrastructure systems depend upon to get built. So it’s the raw material for our whole built world.
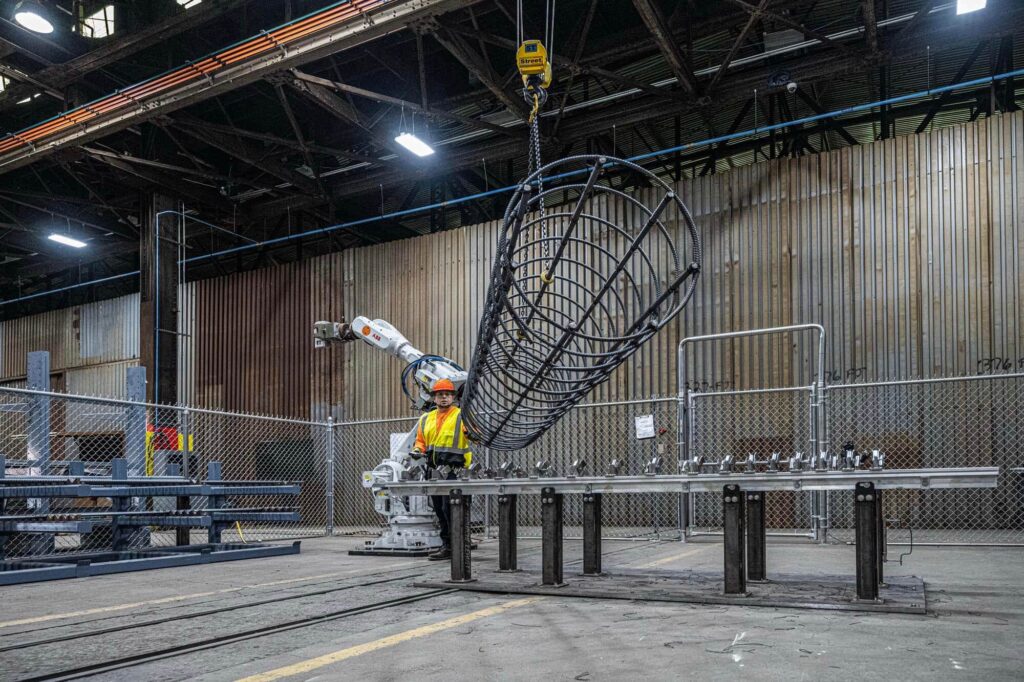
Could you describe the problem you’re tackling with your work?
The problem is really simple supply and demand. I would say that the demand for construction is larger than it’s ever been before, and it’s accelerating. Because the world is urbanizing1, we’re building larger and more complex cities. And so we need infrastructure to support that: power, water, housing, institutional buildings, resiliency on coastlines, etc. We have all of this construction to do, not to mention all of the existing infrastructure that needs to be rehabilitated.
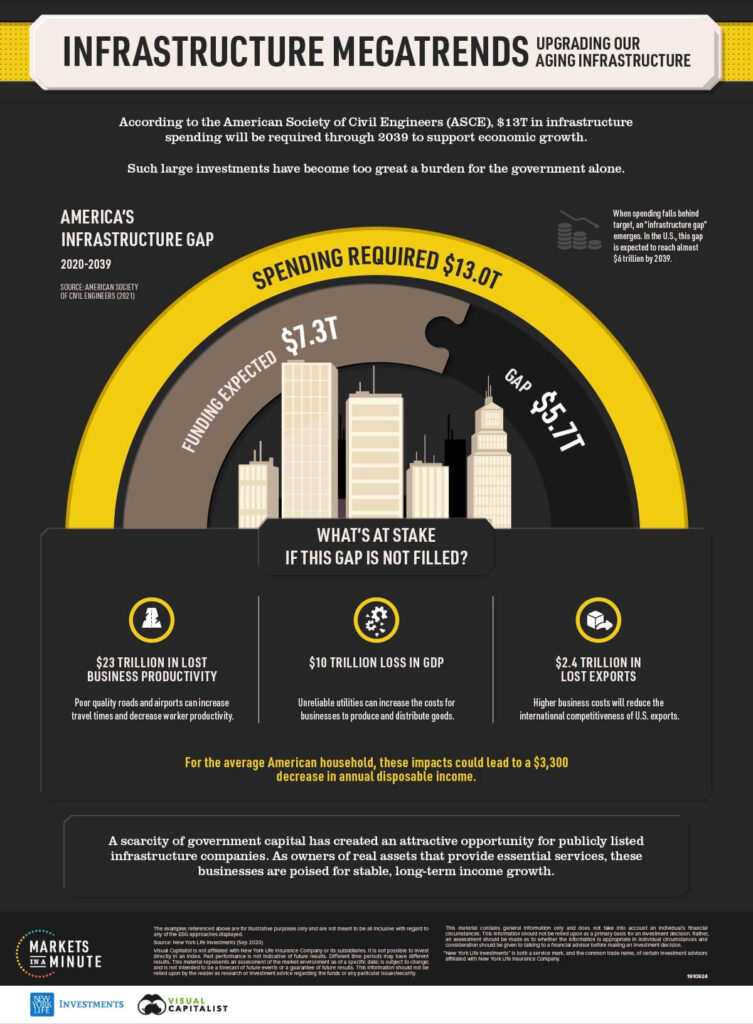
And on the flip side of that, we have a construction industry that has really not adopted a lot of technology or innovation to increase productivity. Certainly not in the way that you see in manufacturing or in really any of the other major industry segments like agriculture or the medical field. And not only has it not kept pace with the productivity gains, you have fewer and fewer people that are actually joining the construction industry.
That creates the problems that we associate with construction all the time: big projects take too long, they go over timeline, they go over budget, they’re fraught with problems and delays and challenges. It’s just getting worse. The last couple of years have exacerbated those problems because COVID has made it more difficult to have a lot of people on a worksite doing their work together. There are labor shortages, supply chain disruptions, and materials cost more. So you need solutions in the construction industry to improve efficiency, to enable us to do more with less.
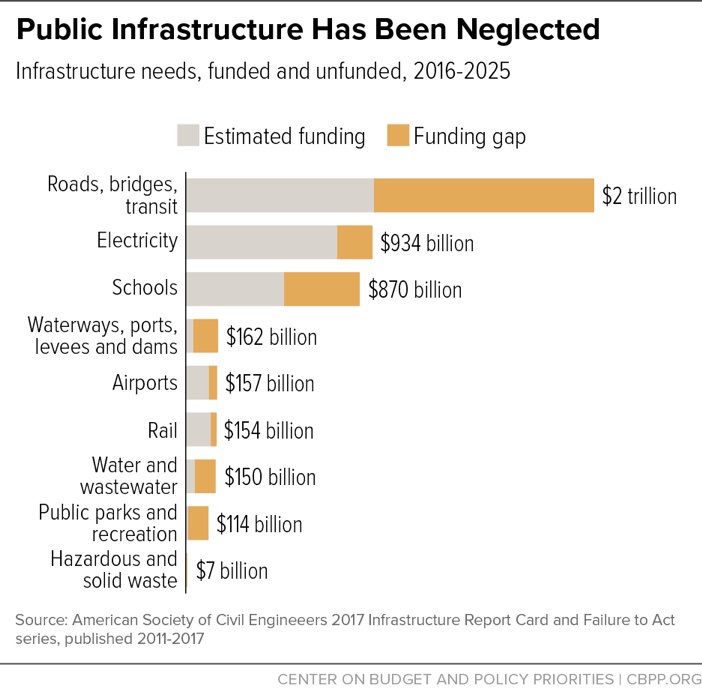
What is it about the construction industry and specifically reinforced concrete that makes the industry so slow to change?
The reason that the construction industry has difficulty changing is because of the risks involved with changing. If you’re a construction company, and you’re doing a certain number of jobs every year, each one of those jobs is really a make or break financial transaction for your company. There is a very high incentive to stick with what works, what has served you well in the past and not take the risk to try something new, which may or may not work.
There’s also the complexity of the way the construction industry is organized. You have different coordinating and contributing parties and stakeholders, different trades, like, concrete companies and rebar companies and carpenters and plumbers and electricians, and, people doing finishing work, and millwork and, all of these different trades that all have to work together in concert and have to align with each other in terms of space, time, and the sequencing of work.
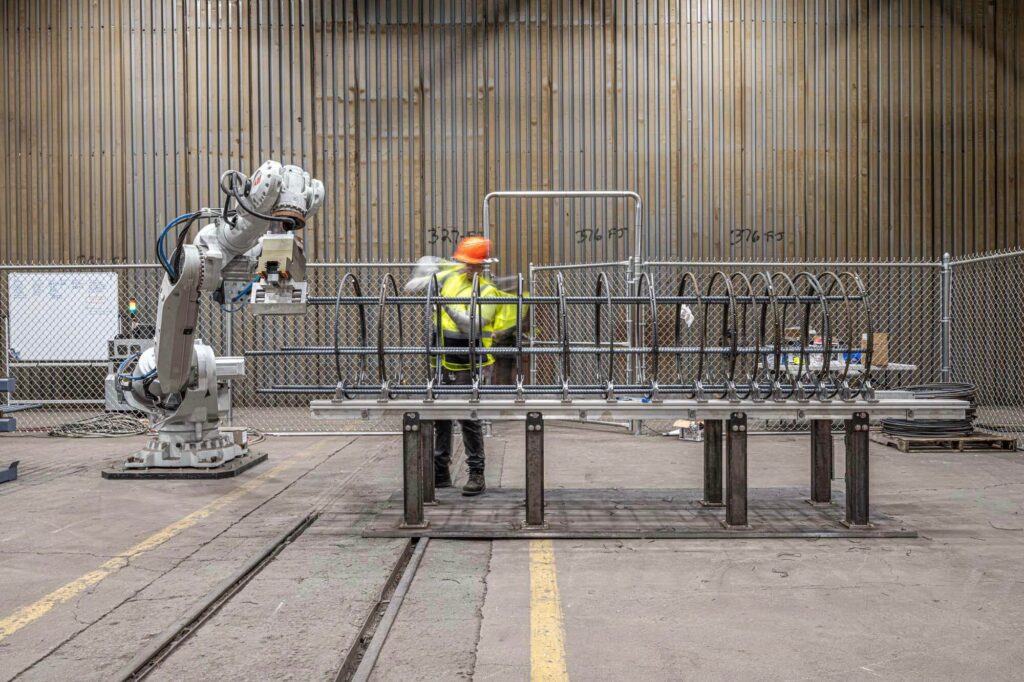
Is there a specific customer case study you could share about the integration process?
There was a project we did in the Philadelphia Navy Yard where they’re basically adding battery storage to the microgrid there. They have renewable energy generation and storage, they have solar, where they’re generating power and then they have battery storage where they can save that power for use, when the sun’s not shining, essentially. And so, we partnered with the EPC that was responsible for designing and building that system and by pre-assembling all the rebar for them so that they didn’t have to do that work on a jobsite. We’re able to save them a really significant amount of labor and time in the build out of that project. And so it’s a very straightforward type of project where our work just immediately accelerates the whole job from start to finish because you’re just not waiting for that rebar to happen.
On a personal note, could you tell us about your work at the Museum of Chinese in Americas?
I live in Chinatown in New York City, and MOCA is down the block. I started volunteering, getting young professionals involved with the museum and doing events for people interested in different career tracks. At the end of the day, these community institutions are also a form of infrastructure; they are a part of living in a community or a city or a neighborhood, in the same way that the subway system is or the hospital is or the university is. Everyone who lives in these areas, and the people who come to visit these areas, depend on these institutions. It’s exciting to engage and contribute to building this cultural infrastructure, in the same way that it is to help develop our physical infrastructure. It’s personally important because my wife is also Chinese, and my kids are half Chinese. It’s a part of my family’s heritage and part of the heritage of the neighborhood that I live in.